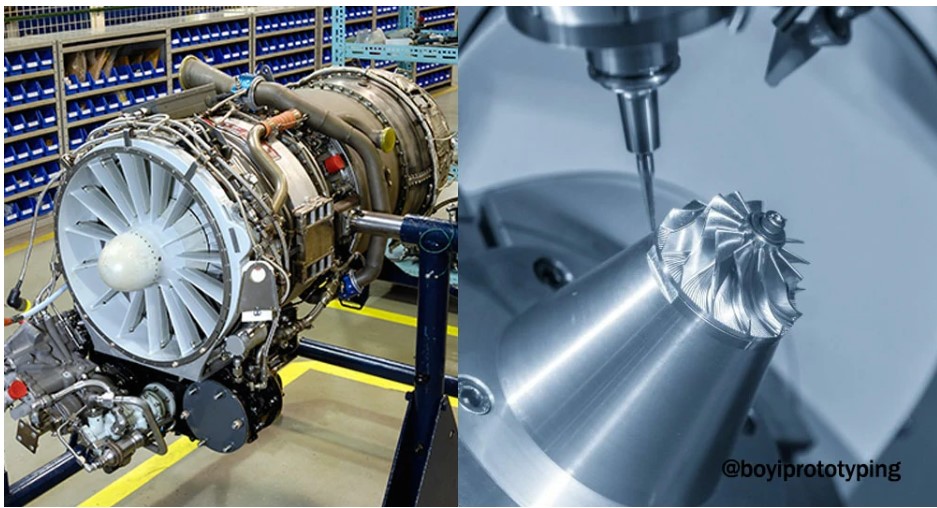
The aerospace industry demands extreme precision, high-strength materials, and strict quality control in component manufacturing. Aerospace CNC machining is a key technology that meets these requirements, with two primary processes: CNC milling and CNC turning. While both methods are essential in aerospace part production, they serve different purposes. CNC milling is ideal for complex geometries, such as aircraft brackets and turbine housings, while CNC turning excels in producing cylindrical components like landing gear struts and engine shafts.
Understanding the differences between CNC milling and CNC turning helps aerospace manufacturers select the right process for each application. This article explores how these machining methods work, their advantages, and their critical applications in aerospace manufacturing.
CNC Mill vs Turn in Aerospace Manufacturing
CNC milling and CNC turning are two core machining processes in aerospace manufacturing, each suited for different types of components. While both rely on computer-controlled precision, they differ in their machining approach, workpiece handling, and the types of parts they produce.
CNC Milling in Aerospace Manufacturing
CNC milling is a subtractive manufacturing process where the workpiece remains fixed or rotated while high-speed rotary cutting tools systematically remove material to form the desired shape. In aerospace applications, CNC milling is particularly useful for fabricating components with intricate geometries, multiple flat or curved surfaces, and internal cavities. This process allows engineers to produce highly precise parts with complex contours and tight tolerances, ensuring structural integrity and aerodynamic efficiency.
One of the most significant advantages of CNC milling in aerospace manufacturing is its ability to operate on multiple axes. While conventional mills function in three axes (X, Y, and Z), advanced aerospace CNC milling machines often incorporate fourth and fifth axes, enabling the machining of intricate features from multiple angles in a single setup. This capability reduces the need for repositioning, minimizing errors and improving overall efficiency.
Key Features of CNC Milling in Aerospace:
- Multi-Axis Capability: Modern CNC milling machines use 3-, 4-, and 5-axis configurations, allowing complex parts to be machined in a single setup. Five-axis milling, in particular, enables precise CNC metal cutting from multiple angles, reducing the need for repositioning and increasing accuracy.
- High Precision and Tight Tolerances: Aerospace components demand extreme accuracy. CNC milling can achieve tolerances as tight as ±0.0001 inches, ensuring parts meet strict aerospace industry standards.
- Capability for Intricate Geometries: CNC milling excels at creating detailed features, including slots, pockets, contours, and undercuts that would be difficult to achieve with other machining processes.
- Material Versatility: CNC milling can process a wide range of aerospace-grade materials, including aluminum (lightweight yet strong), titanium (high strength-to-weight ratio), Inconel (heat-resistant), and advanced composite materials used in modern aircraft and spacecraft.
- Automated and High-Speed Machining: Advanced CNC milling systems integrate high-speed spindles and automatic tool changers, optimizing machining efficiency while maintaining precision.
- Effective for Large and Small Parts: Whether manufacturing large structural components or small precision parts, CNC milling provides the flexibility needed for diverse aerospace applications.
Common Aerospace Parts Produced with CNC Milling:
- Aircraft Brackets: Structural brackets that support and connect various aircraft components.
- Fuselage Frames: Load-bearing structures that form the aircraft's body.
- Bulkheads: Internal support structures that enhance an aircraft's strength and integrity.
- Turbine Casings: Protective enclosures for jet engine turbines.
- Compressor Housings: Components that house and guide airflow through jet engine compressors.
- Fuel Injector Bodies: Precisely machined housings for fuel injection systems in aircraft engines.
- Landing Gear Components: Support structures for aircraft landing systems, including strut housings and mounts.
- Precision Mounting Plates: Critical plates used in avionics and navigation systems to secure electronic components.
CNC Turning in Aerospace Manufacturing
CNC turning is a machining process where the workpiece rotates at high speeds while a stationary cutting tool removes material to achieve the desired shape. This method is particularly effective for producing round, cylindrical, or conical aerospace components with exceptional precision. Since turning operations involve continuous rotation, the process naturally results in smooth, concentric surfaces, reducing the need for secondary finishing processes.
In aerospace manufacturing, CNC turning plays a vital role in producing components that require precise diameters, tight tolerances, and superior surface finishes. The process allows for high-speed material removal, making it highly efficient for machining long shafts, rods, and other rotationally symmetric parts. CNC lathes used in aerospace applications often feature multi-axis configurations, including live tooling capabilities, which enable additional milling and drilling operations without removing the part from the machine.
Key Features of CNC Turning in Aerospace:
- Superior Surface Finish: Since the workpiece rotates continuously, CNC turning produces exceptionally smooth and precise cylindrical surfaces, reducing the need for additional polishing or finishing.
- Efficient for Cylindrical Parts: CNC turning is the fastest and most cost-effective method for machining round or tubular components with high precision.
- High Accuracy and Repeatability: CNC turning machines can achieve tight tolerances, ensuring consistency in aerospace components where even minor deviations can affect performance and safety.
- Capability for Complex Profiles: Modern CNC turning centers often include live tooling and multi-axis configurations, allowing additional milling, drilling, and threading operations in a single setup.
- Effective for Hard-to-Machine Materials: Aerospace applications require durable materials like titanium, stainless steel, and Inconel. CNC turning can process these materials efficiently, ensuring high structural integrity.
- Optimized for Mass Production: CNC turning is ideal for manufacturing high-volume aerospace components with minimal variation, making it a preferred process for producing standardized parts.
Common Aerospace Parts Produced with CNC Turning:
- Landing Gear Struts: Cylindrical support structures that absorb impact during aircraft landings.
- Hydraulic Pistons: Precision-machined pistons used in aircraft hydraulic systems for movement and control.
- Turbine Shafts: Rotating shafts that transmit power within jet engines.
- Fuel Nozzles: Components that precisely control fuel delivery in jet engines.
- Exhaust System Components: Cylindrical parts designed to manage and direct high-temperature engine exhaust gases.
- Precision Fasteners: Custom nuts, bolts, and screws that hold critical aerospace components together.
- Aerospace Bushings: Cylindrical linings used to reduce friction and wear in moving aircraft parts.
Key Differences in Aerospace Applications
Both CNC milling and CNC turning are essential in aerospace manufacturing, often complementing each other in the production process. The choice between the two depends on the geometry, function, and material of the component being manufactured.
Aspect | CNC Milling | CNC Turning |
Workpiece Shape | Best for complex, non-cylindrical shapes with multiple surfaces | Best for round, symmetrical parts with consistent diameters |
Machining Approach | Workpiece remains stationary or rotated while the cutting tool moves in multiple directions | Workpiece rotates while a stationary cutting tool removes material |
Precision & Tolerances | High precision for multi-surface parts with intricate details | Exceptional accuracy for cylindrical components with smooth finishes |
Production Speed | Slightly slower due to complex tool movements and multi-axis machining | Faster for cylindrical parts, as continuous rotation speeds up material removal |
Material Versatility | Suitable for aluminum, titanium, Inconel, and composites | Works efficiently with aerospace-grade steels, titanium, and high-strength alloys |
Common Aerospace Components | Aircraft brackets, fuselage frames, bulkheads, turbine casings, compressor housings, fuel injector bodies, landing gear components, precision mounting plates | Landing gear struts, hydraulic pistons, turbine shafts, fuel nozzles, exhaust components, precision fasteners, aerospace bushings |
Turbine Component Production
Aerospace turbines are among the most critical components in jet engines, responsible for converting high-temperature, high-pressure gases into mechanical energy to propel aircraft. Precision manufacturing is essential, as turbine components must endure extreme temperatures, high rotational speeds, and mechanical stress while maintaining optimal efficiency and durability. Two key components of turbine systems—blades and nozzles—require advanced CNC machining techniques to achieve the required aerodynamic and structural integrity.
Blade Machining Methods
Turbine blades play a vital role in the efficiency and performance of jet engines, as they are responsible for extracting energy from the high-speed airflow. These blades must be manufactured with extreme precision to ensure aerodynamic efficiency, minimize drag, and withstand harsh operating conditions.
CNC Milling for Turbine Blades
CNC milling is the primary method for producing turbine blades due to its ability to create complex aerodynamic profiles with high accuracy. Using 5-axis CNC milling, manufacturers can machine intricate curved surfaces in a single setup, reducing errors and improving efficiency. The process begins with a solid metal billet—often titanium, Inconel, or nickel-based superalloys—which is gradually shaped using specialized cutting tools.
Key features of CNC milling for turbine blades:
- 5-axis simultaneous machining allows precise contouring of aerodynamic blade surfaces.
- High-speed machining ensures smooth surface finishes with minimal tool marks.
- Adaptive cutting strategies reduce material stress and prevent microcracks in superalloys.
- Automated tool changers enable rapid cutting of different sections, from the airfoil to the root and shroud.
To enhance durability, CNC-milled turbine blades may undergo additional post-processing steps such as polishing, surface coating (thermal barrier coatings), and electrochemical machining (ECM) to refine the contours without introducing mechanical stress.
CNC Turning for Turbine Blade Roots and Mounting Features
While the main airfoil profile is machined using milling, CNC turning plays a crucial role in producing the blade root and mounting features, which attach the blade to the turbine disk. The root design is often a fir-tree or dovetail shape, requiring precise tolerances to ensure a secure fit and prevent loosening under extreme rotational forces.
CNC turning is also used for trailing edge cooling features and fillet radii, which help optimize airflow and thermal management. The lathe rotates the workpiece while a cutting tool removes material to achieve the desired shape.
Key features of CNC turning for turbine blades:
- High-precision contouring for fir-tree and dovetail roots.
- Efficient material removal to shape cylindrical and symmetrical sections.
- Live tooling integration to add slots and cooling holes without secondary operations.
- Consistent concentricity for uniform stress distribution in rotating parts.
Nozzle Manufacturing
Turbine nozzles, also known as stator vanes or guide vanes, are fixed components that direct airflow onto turbine blades, optimizing energy conversion. These nozzles must be manufactured with precise aerodynamic profiles to regulate airflow and minimize turbulence, ensuring peak engine efficiency.
CNC Milling for Nozzles
Similar to turbine blades, CNC milling is widely used for shaping nozzle vanes. Nozzles typically feature airfoil-shaped cross-sections, complex curvature, and mounting features for precise alignment within the turbine. 5-axis CNC milling is ideal for machining these intricate geometries, allowing engineers to achieve smooth surfaces that enhance airflow.
Key features of CNC milling for turbine nozzles:
- Multi-axis cutting enables smooth transitions between concave and convex surfaces.
- Precision finishing ensures uniform thickness and surface quality, reducing drag.
- Custom tool paths optimize cutting efficiency for superalloys and ceramic-coated materials.
CNC Turning for Circular Nozzle Rings
While individual nozzle vanes are milled, larger circular nozzle rings—which hold multiple vanes in place—are often produced using CNC turning. These rings must have perfect concentricity and smooth internal surfaces to maintain turbine efficiency.
Key features of CNC turning for nozzle rings:
- High-speed turning achieves precise diameters with tight tolerances.
- Live tooling integration enables additional milling for mounting features and bolt holes.
- Surface finishing techniques enhance wear resistance and durability.
Structural Part Creation
Structural components in aerospace must be lightweight yet extremely strong to handle high stress and pressure loads while maintaining fuel efficiency. These parts often require precision machining to ensure exact dimensions, tight tolerances, and reliable performance in harsh conditions. CNC milling and CNC turning play crucial roles in manufacturing critical structural elements such as bulkheads, fasteners, wing spars, and fuselage frames.
Bulkhead Machining
Bulkheads are key structural reinforcements inside an aircraft’s fuselage. They provide strength and rigidity, dividing the aircraft into sections and supporting internal components. These parts must be both lightweight and high-strength, which is why aerospace manufacturers primarily use aluminum, titanium, or composite materials for bulkhead production.
CNC Milling for Bulkheads
CNC milling is the primary method for machining bulkheads due to their large, complex shapes and the need for precise cutouts and weight-reducing pockets. Bulkheads often have integrated mounting points, reinforcing ribs, and aerodynamic contours, which require multi-axis machining.
Key features of CNC milling for bulkheads:
- 5-axis capability ensures precise contouring of bulkhead geometry.
- High-speed machining removes excess material efficiently while maintaining strength.
- Precision pocketing reduces weight while maintaining structural integrity.
- Adaptive tool paths minimize vibration and stress in the material.
The machining process starts with a solid aluminum or titanium billet, which is then milled down to its final shape using high-speed carbide or diamond-coated cutting tools. CNC milling creates precise holes, slots, and attachment points to integrate bulkheads into the fuselage structure.
After machining, surface treatments such as anodizing, chemical conversion coating, or thermal treatments are applied to enhance corrosion resistance and fatigue strength.
Fastener Production
Fasteners are one of the most critical components in aerospace assembly, ensuring that different parts of the aircraft are securely joined. Aerospace fasteners include bolts, rivets, screws, and pins, often made from titanium, stainless steel, or aerospace-grade aluminum for high strength and corrosion resistance.
CNC Turning for Fasteners
Fastener production relies heavily on CNC turning because fasteners are cylindrical components that require precision threading, tight tolerances, and uniform diameters. The CNC lathe rotates the raw metal bar stock while a cutting tool shapes it into standard or custom fastener designs.
Key features of CNC turning for aerospace fasteners:
- High-speed production enables mass manufacturing of uniform fasteners.
- Precision threading ensures secure, vibration-resistant connections.
- Live tooling capabilities allow for additional milling operations like hex heads or grooves.
- Automated feed systems improve efficiency in high-volume production.
Common aerospace fasteners produced with CNC turning include:
- Studs – Used in engine assemblies and structural connections where high shear and tensile strength are required.
- Sleeve nuts – Provide secure fastening in high-vibration environments, such as landing gear and engine mounts.
- Barrel nuts – Used in aircraft structures to fasten panels and components while distributing loads efficiently.
- Shear pins – Designed to break under excessive load to protect critical systems from damage, commonly used in control linkages.
- Dowel pins – Ensure precise alignment of components in engine casings and structural assemblies.
- Tapered pins – Used in high-stress aerospace applications where strong, precise alignment is needed.
- Specialty captive fasteners – Designed for access panels and removable components, preventing loss during maintenance.
Conclusion
CNC milling and CNC turning are vital in aerospace manufacturing, each specializing in different component types. CNC milling is ideal for complex, contoured parts like turbine blades and bulkheads, while CNC turning excels at cylindrical components such as shafts and fasteners.
Advanced 5-axis milling, precision turning, and automation ensure high accuracy, material efficiency, and structural integrity. As aerospace technology evolves, CNC machining remains essential for producing lighter, stronger, and more aerodynamic aircraft components with the precision required for safety and performance.
Leave a Reply
You Might Like Also
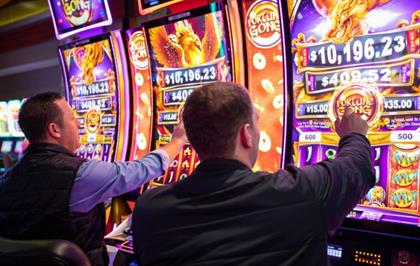
Wow388 Casino Everything You Need to Know
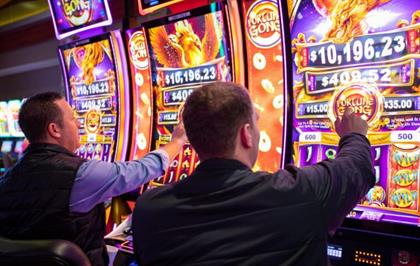
Wow388 Casino Everything You Need to Know
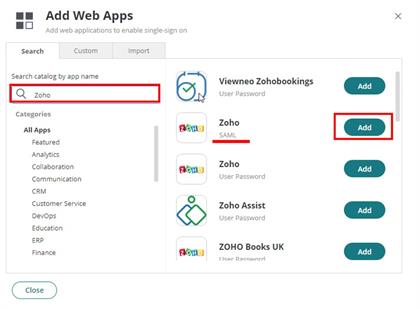