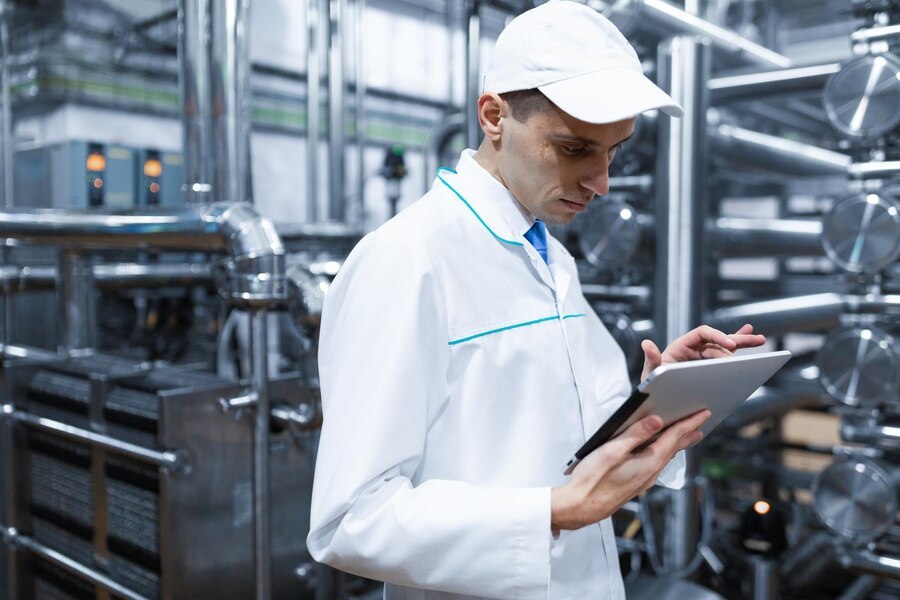
Quality control techniques are crucial for businesses to maintain product excellence and customer satisfaction. By implementing robust quality control measures, organizations can ensure that their products meet high standards, reduce defects, and enhance their brand reputation.
Understanding Quality Control
Quality control is the systematic process of monitoring and regulating various aspects of production to ensure products correspond to specified standards of quality. It encompasses a wide array of techniques and methodologies that are meant to maintain product quality.
Key Quality Control Techniques
Statistical Process Control (SPC)
Statistical Process Control is an effective tool in the control of manufacturing processes. SPC uses statistical methods to analyze process data and discover areas of potential problems before they become full-blown issues. By monitoring key metrics and imposing control limits, the business will take steps to rectify deviations from performance levels.
Total Quality Management
Total Quality Management (TQM) is a comprehensive approach to quality involving every employee within an organization. Continuous improvement focuses on customer satisfaction and employee empowerment. Through a culture of quality, TQM can make significant improvements in the quality of products and performance in an organization.
Six Sigma
Six Sigma is a data-driven method that focuses on minimization of defects and variability in a process. It uses statistical tools to solve problems critically. With more opportunities for the reduction of defects to just 3.4 per million, Six Sigma gives an organization an excellent quality standard.
Design of Experiments (DOE):
Defined To define the systematic planning of experiments to identify the key factors influencing product quality.
- Benefits: This also optimizes product design, reduces development time, and minimizes costs.
- Application in Life A pharmaceutical company uses the DOE to find out the optimum ingredient combination and process conditions that would make sure a drug is effective in maximizing drug efficacy and minimizing side effects.
- FMEA
- FMEA: Identification of failure modes in the company's process or product and review of possible impact.
Benefits Prioritize and prevent costly failures of risk mitigation.
Real-world Application: An automobile manufacturer applies the FMEA to the car engine assembly line and identifies loose bolts and faulty sensors as possible causes of engine failure.
Control Charts:
This application monitors process variability in time to identify shifts or trends that may indicate potential quality issues, such as the signs of defects arising due to quality-related problems.
They support early detection of problems, reduction in waste, and process stability improvement.
Real-world Application: A semiconductor company monitors silicon wafer thickness on the factory floor using control charts in order to maintain quality consistency.
Employee Training
It is crucial to empower the employees to utilize quality control practices effectively. Strategies Training at regular intervals for statistical process control, problem-solving, and quality methods.
Supplier Quality Management
It is essential to ensure that the suppliers deliver good-quality materials and parts.
Strategies: Develop effective qualifications of suppliers, conduct regular audits, and work together with suppliers to enhance their quality management systems.
Customer Feedback and Complaint Management
- The Importance: As a source of valuable information on how the product performs and how customers expect them
- The Strategies: Implementing effective mechanisms of taking customer feedback, managing complaints, address and utilising the customers' feedback for constant improvement
- Role of Technology in Quality Control
- Quality Management Software: Automates data collection and analysis, streamline quality processes and produces real-time reports.
- IoT/ Predictive Maintenance: Maintain equipment condition, know the expected future failures to avoid excessive stoppages and poor quality products.
- AI/ Machine Learning: Analyze large datasets to identify trends, anomalies, and opportunities for improvement.
Conclusion
Effective quality control techniques, such as SPC, TQM, Six Sigma, RCA, and quality audits, help businesses achieve superior product quality, enhance customer satisfaction, and create a competitive advantage. Amrepinspect offers quality inspection services to help organizations meet their quality goals.
FAQs
Why is quality control important?
Quality control is significant for maintaining consistency in the production of goods without defects and providing improved customer satisfaction.
What strategies can one adopt to enhance quality?
Quality control through SPC, TQM, and Six Sigma ensures a much better quality product.
What are the most important reasons for quality control?
Reduced costs and customer satisfaction are key benefits of quality control. This leads to an enhanced brand reputation.
How can Amrepinspect help improve quality?
Amrepinspect offers multiple quality inspection services such as product testing, material inspection, and supplier audit so that business can guarantee product excellence.
Leave a Reply
You Might Like Also
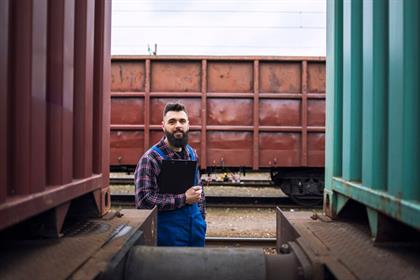
Key Facts About Border Factories: What You Need to Know
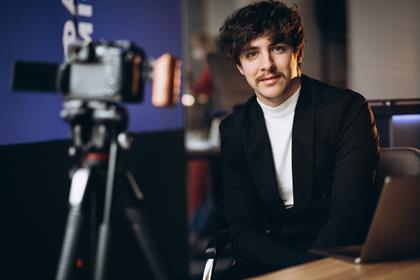