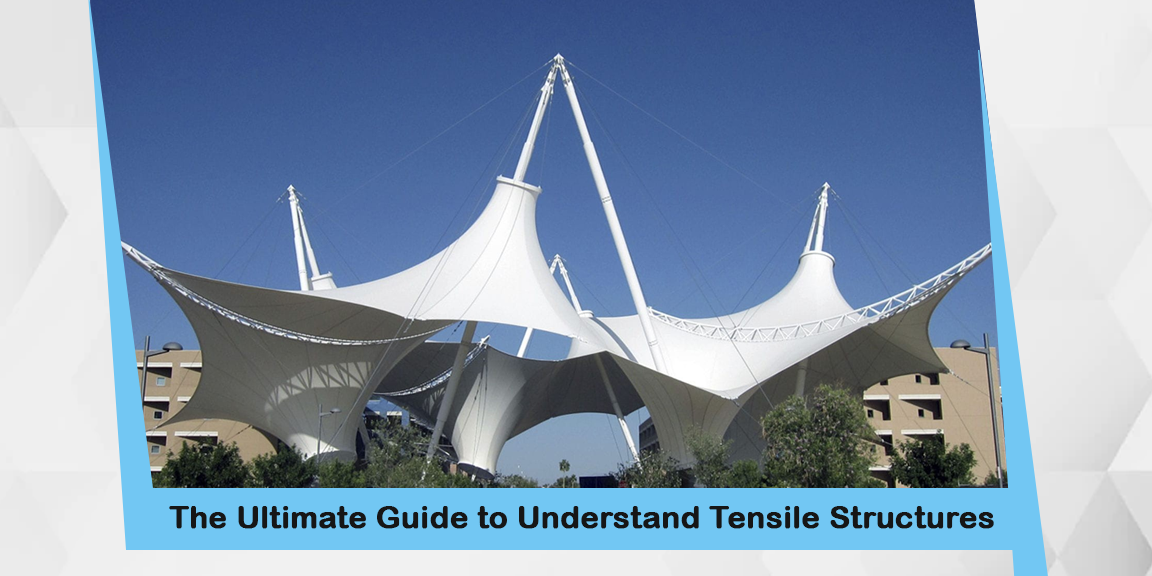
A tensile structure is made up of exclusively tension-carrying parts with neither compression nor bending. Tensile is not to be confused with tensegrity, a structural form that includes both tension and compression aspects. The most frequent sort of thin-shell construction is a Tensile Structure. Compression or bending elements, such as masts (as in The O2, previously the Millennium Dome), compression rings, or beams, support most tensile constructions.
It is common to use Tensile Membrane Structures as roofs since they can span great distances inexpensively and efficiently. Tensile membrane structures can also be employed as whole buildings, with sports facilities, warehousing and storage facilities, and exhibition halls being some of the most common examples.
Classification of Tensile Membranes
Membrane-tensioned structures, mesh-tensioned structures, and pneumatic structures are the three primary classifications in the subject of tensile construction systems. The first concerns constructions in which a membrane is kept in place by cables, allowing tensile stresses to be distributed through the membrane's form. The second type of structure is one in which the intrinsic forces are carried via a network of cables and transmitted to different parts, such as sheets of glass or wood. A protective membrane is supported by air pressure in the third case.
Tensile Membrane Materials
Tensile membranes are usually made of coated or proven textiles. Nonwovens of various sorts are used in a variety of applications. There are a variety of natural and synthetic fibres available today that could be utilized to make membranes. However, the normal demands on structural textile membranes, as well as the need for a series of detailed experiments with the material and its joints, have resulted in a limited selection of fibres for general usage.
The textiles aren't waterproof in the first place. Furthermore, the majority of the fibres will be harmed by environmental factors such as sunlight radiation. This frequently results in a loss of strength and flexibility, among other things. As a result, the fabrics must be proven or coated. For cotton and cotton/synthetic materials, proving is the preferred treatment. The PVC coating is the most frequent solution for Polyester and Aramid fabrics, whereas PTFE coating is prevalent for glass fibre materials.
The coating system must be well suited to the fabric's fibres: on the one hand, the coatings are applied to the fabrics at high temperatures that the fibres must be able to withstand; on the other hand, chemical and mechanical adhesion to the fabric is critical for shear stiffness and, with it, the load-bearing capacity of many structural details. The strength of a membrane is determined by the yarn used, the weave employed, and the fabric count utilized. Tensile strength of up to 200 kN/m can be achieved with PVC/Polyester and PTFE/Glass materials that can be purchased from stock. On request, quality of up to 300 kN/m can be Tensile Structure manufacture. PVC-coated Aramids have strong characteristics that can exceed 600 kN/m. However, the latter is only used in exceptional circumstances because of its exorbitant cost and lack of transparency.
The following are the most common types of tensile fibres:
PVC Coated Polyester: For both permanent and temporary tensile fabric structures, PVC-coated polyester might be a good choice. When compared to PTFE coated glass cloth and ETFE, PVC-coated polyester is noted for its superior strength, flexibility, translucency, and affordability. UV stabilizers, fire retardant chemicals, and anti-fungicides are all included in the PVC coating that is sprayed on polyester. Polyester fabrics with a PVC coating have a structural lifespan of more than 20 years
PTFE Coated Glass Cloth: DuPont invented PTFE coated glass cloth in the 1960s, and it has been used to make tensile fabric structures since the early 1970s. The material's original life expectancy was 25 years; however, this has already been exceeded, with current projections ranging between 30 and 50 years.
ETFE: While ETFE is a film rather than a fabric, it is worth mentioning because it is frequently employed as a structural glass replacement and is quickly expanding in its uses. If thermal insulation is a top priority for your project, ETFE is a great option.
Types of Tensile Structure
The many types of tensile structures are created on the plane where the tensile forces are acting. Tensile constructions are classified into the following categories based on this:
- Linear Tensile Structures
Linear tensile structures are made up of members that are all subjected to linear tensile forces. The compression members support the linear members, while the tensile members carry the majority of the weight. Cable-suspended bridges are a common example of these structures. The major pillars serve as compression members, however, the entire load is carried by the tensioned cables.
The following types of linear tensile structures are classified:
- Suspension bridges
- Draped cables
- Cable-stayed beams or trusses
- Cable trusses
- Straight tension cables
2. Three-Dimensional Tensile Structures
Three-dimensional tensile constructions are made up of parts that are mostly in tension, with compression transferred to a central mast and down into the ground. Three-dimensional tension is most commonly seen in sports arenas, which usually function as Tensile roof Structure for these structures. The following are examples of three-dimensional tensile structures:
- Bicycle wheel;
- 3D cable trusses
- Tensegrity structures
3. Surface-Stressed Tensile Structures
Surface-stressed tensile structures are similar to the other two types of tensile structures, with the exception that the surface components are tension-bearing. A protective membrane is maintained by air pressure in this fabric construction, which is commonly used in building facades and dome tents. The following are examples of surface-stressed tensile structures:
- Prestressed membranes
- Pneumatically stressed membranes
- Gridshell Fabric structure
Shapes of Tensile Fabric Structure
A perfect shape is necessary as per the requirement. There are four basic shapes used in the tensile fabric structure are as follows:
Conical Tension Structure
The tent-like shape of a conical tension membrane structure makes it highly useful for covering huge areas. Single or more masts can be used in conical designs. Membranes are tensioned between a ring at the pinnacle and the lower perimeter support columns in both design alternatives. Cones are especially useful in places where high rain or snow load limits must be met.
Hypar or Anticlastic Structure
Hyper, (hyperbolic paraboloid) forms are remarkable for their excellence with shape retention and water runoff. They are one of the most prevalent of all tensioned membranes due to their visually pleasing look. The stability of these structures is based on two opposing curvatures, also known as anticlastic. Shades can be provided over seating areas or high-traffic corridors with this style of structure.
Parallel Arch or Barrel Vault Structure
These symmetrical curving parallel arch designs create a highly effective tensioned membrane canopy that may cover large areas, such as a sports stadium, or smaller sections, such as an entryway. Due to the repeating nature of the design and material savings, a barrel vault system can be a very cost-effective approach to incorporate tensile membrane on a project, depending on the spans.
Cable Net & Membrane Structure
3D cable net or cable grid structures are an efficient lightweight tensile architecture solution for long-span tensile membrane roofing applications, such as those found in stadiums or huge venues.
Advantages of Tensile Structure
Owners and developers all around the world have found the benefits of tensile fabric building constructions over standard building materials. A tensile fabric structure may be the appropriate answer for an entertainment facility such as an amphitheatre, walkway coverage for travellers at transit stations, or a structure to make your athletic fields ready for year-round action. The following are some of the benefits of tensile membrane structures:
- Tension membrane structure installation is generally faster and more cost-effective than standard construction projects when correct construction procedures are in place by design-build speciality contractors for tensile architecture.
- Tensile fabric building constructions provide an abundance of daytime light underneath due to the transparency associated with nearly all fabric alternatives, making it an inviting and comfortable space below.
- Modern fabrics offer advantages like UV protection and improved wind resistance, in addition to being more weather-proof and lighter in weight than sticks and animal skins. They're also protected against UV rays with UV-resistant coatings.
- Tensioned membrane structures allow architects, designers, and engineers to experiment with form and build aesthetically fascinating and iconic structures due to the fabric membrane's unique flexible qualities.
- When it comes to covering huge sections of space, the membrane's lightweight makes it a cost-effective alternative for long-span applications while also providing column-free space. As a result, when compared to typical building goods, tensile membrane requires fewer structural steel supports, lowering project costs for building owners.
- Because the membrane weighs so little in tensile structures, the amount of structural steel required to support the membrane is likewise small. As a result, tensile structures have a substantially lower weight and overall cost than traditional roofing systems. With the use of stainless steel, additional usable space free of columns becomes accessible. Due to the structure's little weight, it will not be subjected to significant acceleration forces during seismic activity.
- The membrane material can tolerate temperatures ranging from -40 to +70 degrees Celsius. Companies provide warranties for their fabrics, and these structures typically have a minimum life expectancy of roughly 25 years.
- Tensile structure erection takes less than a week to complete because all patterning and fabrication work is done in warehouses and the structure is assembled on-site. The construction period refers to the time it takes to erect the structure, which can be cut in half by employing innovative construction equipment and techniques.
Final Note
Membrane structures can be designed, evaluated, and built in any shape or form. It gives the designer more room to experiment with alternative shapes. Artificial lights can be included in the membrane fabric, giving it a new aesthetic dimension. It's not only a budget-friendly option, but it's also aesthetically beautiful. Tensile structures are a relatively new concept that has only recently entered the Indian construction scene and is swiftly gaining favour. The regions where the tensile structure outperforms conventional structures are as follows.
Leave a Reply
You Might Like Also
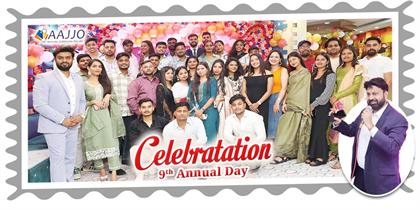
Another Year of Excellence: Celebrating Aajjo’s 9th Annual Day
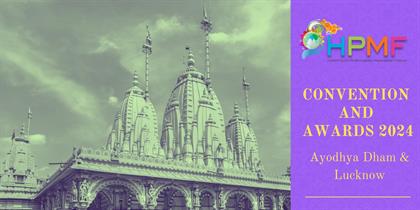
Witness Hospitality Excellence in Ayodhya Dham & Lucknow: HPMF Convention 2024
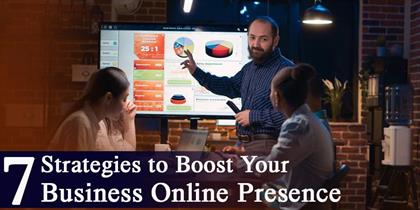
7 Tips to Grow Your Business Online
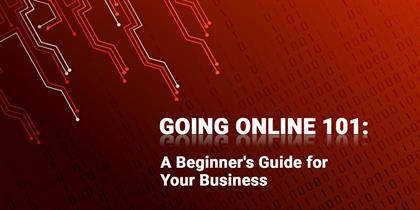