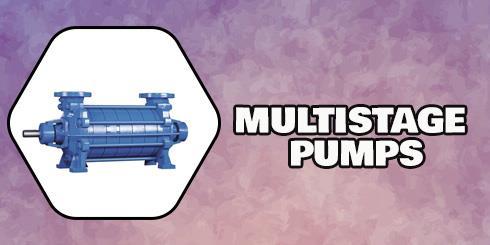
In the world of moving liquids efficiently, Multistage Pumps play a crucial role, especially when dealing with high-pressure situations. Unlike their simpler single-stage counterparts, these pumps are like unsung heroes, capable of generating significant pressure thanks to their smart engineering.
Understanding Centrifugal Pumps:
Imagine a well-organized relay race for liquids. In a single-stage pump, the liquid starts from one point, gets a boost from the impeller, and quickly reaches its destination. Now, think of a multistage pump as a relay with multiple legs. The liquid moves from one impeller to the next, gaining energy at each step, until it successfully reaches the end, achieving the desired pressure. The series of impellers is what makes Centrifugal Pumps unique.
How Centrifugal Pumps Work:
Centrifugal Pumps work in a detailed way, and each part has an important job. Let's break it down into simpler terms:
Rotor:
This is like the pump's heart. It's a fast-spinning blade that gives energy to the liquid it's pumping. Think of it as the first step that gets things moving.
Diffusion Mechanism:
This part doesn't move; it stays still. Its job is to change the energy from the spinning blade into strong pressure. This change is really important for making sure the liquid can go through all the stages of the pump effectively.
Reflux Conduit:
This is like a guide for the pressured liquid. It helps direct the liquid from one part of the pump to the next. Imagine it as a path that keeps the liquid moving smoothly between stages.
Here's how it all works:
- When the liquid starts its journey into the pump, the first spinning blade makes it go faster.
- The still part (diffusion mechanism) takes this speed and turns it into strong pressure.
- The pressured liquid then travels through the guide (reflux conduit) to the next spinning blade.
So, it's like a step-by-step process where each part has a specific job to make sure the liquid moves smoothly and gets pressurized along the way.
Advantages of Centrifugal Pumps:
High Pressure: Centrifugal Pumps excel in tasks that require managing high pressures, like water supply, irrigation, firefighting, and oil and gas pipelines.
Compact Design: Compared to single-stage pumps with similar pressure capacities, Centrifugal Pumps often have a more compact and lightweight design, making them suitable for space-constrained installations.
Energy Efficiency: Despite needing more power due to additional impellers, Centrifugal Pumps are often more efficient, leading to lower operational costs in the long run.
Adaptability: Available in various configurations and materials, Centrifugal Pumps can handle a wide range of liquids and operating conditions.
Applications of Centrifugal Pumps:
Centrifugal Pumps are really important in many different industries because they can do a lot of different jobs. One big way they help is with moving and treating water. In places where people live, these pumps help push water through pipes in cities and move water to treatment plants. They also help make saltwater usable in desalination processes.
For farming, Centrifugal Pumps are super useful in making sure there's enough water for big fields. They're reliable and work well, which helps farmers grow a lot of crops.
In case of fires, these pumps are heroes too. They provide the strong water pressure needed to fight fires and keep sprinkler systems working. This is crucial to save property and lives during emergencies.
In the oil and gas industry, Centrifugal Pumps are like superheroes for moving oil and gas through really long pipes. They're strong and can handle the challenges of transporting these resources over long distances.
Chemical plants also use these pumps to manage chemicals in tough conditions – high pressure and temperature. This helps keep things safe and efficient in making various products.
When it comes to making power, Centrifugal Pumps are important in power plants. They feed boilers and help transfer liquids in systems that use heat from the Earth (geothermal energy). This helps us get renewable energy.
So, these pumps do a lot of jobs in different industries – moving water, helping with farming, fighting fires, transporting oil and gas, managing chemicals, and making power. They're like all-in-one helpers in making sure things work well in different parts of our lives.
Choosing the Right Multistage Pump:
Selecting the right multistage pump for a specific application involves careful consideration of various factors:
Flow Rate: Determining the needed volume of liquid to be pumped per unit of time.
Head: Identifying the pressure difference the pump must overcome.
Liquid Characteristics: Considering the viscosity, density, and temperature of the liquid.
Material Compatibility: Ensuring the pump materials are compatible with the liquid and operational conditions.
Power Requirements: Assessing the power needed for the pump to function optimally.
Final Thoughts:
Centrifugal Pumps stand out as essential tools in tasks requiring high pressure. Their ability to generate substantial pressure, along with their compact design and versatility, makes them indispensable in various industries. The next time you face a demanding liquid task, remember the effectiveness of Centrifugal Pumps – the unsung heroes that propel liquids to new heights and pressures.
FAQs
What makes Centrifugal Pumps different from single-stage pumps?
Centrifugal Pumps operate like a relay with multiple stages, accumulating energy at each step, while single-stage pumps have a simpler one-step process.
Where do Centrifugal Pumps excel in terms of applications?
Centrifugal Pumps are ideal for tasks requiring elevated pressures, such as water supply, irrigation, firefighting, oil and gas pipelines, and more.
What are the key components of a multistage pump?
The essential parts include the rotor (a fast-spinning blade), the diffusion mechanism (converting kinetic energy to pressure), and the reflux conduit (guiding pressurized liquid to the next stage).
How do Centrifugal Pumps achieve high pressure?
The liquid undergoes a sequence of impeller stages, with each stage increasing the pressure, allowing Centrifugal Pumps to achieve heads and pressures beyond single-stage capacities.
What advantages do Centrifugal Pumps offer in terms of design?
Centrifugal Pumps often have a more compact and lightweight design compared to single-stage pumps with similar pressure capacities, making them suitable for space-constrained installations.
What industries benefit from the adaptability of Centrifugal Pumps?
Centrifugal Pumps find applications in various industries, including water conveyance and treatment, irrigation, fire suppression, oil and gas transport, chemical processing, and power generation.
How can I choose the right multistage pump for a specific application?
Consider factors such as flow rate, head, liquid characteristics, material compatibility, and power requirements. Consulting with a pump engineer is recommended for optimal selection.
Do Centrifugal Pumps contribute to energy efficiency despite needing more power?
Yes, Centrifugal Pumps often have heightened efficiency, leading to diminished operational costs over the long term.
Leave a Reply
You Might Like Also
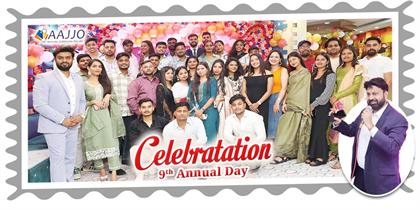
Another Year of Excellence: Celebrating Aajjo’s 9th Annual Day
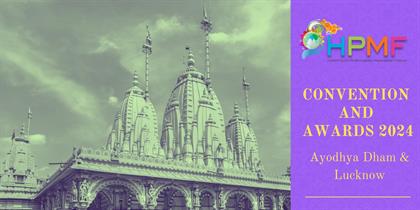
Witness Hospitality Excellence in Ayodhya Dham & Lucknow: HPMF Convention 2024
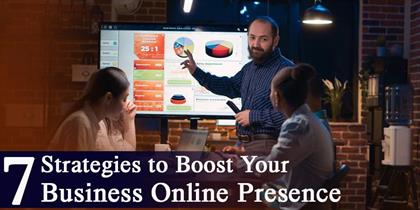
7 Tips to Grow Your Business Online
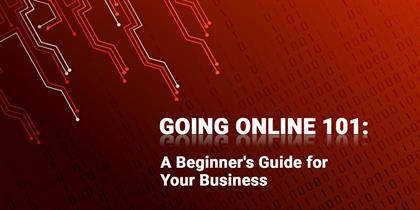