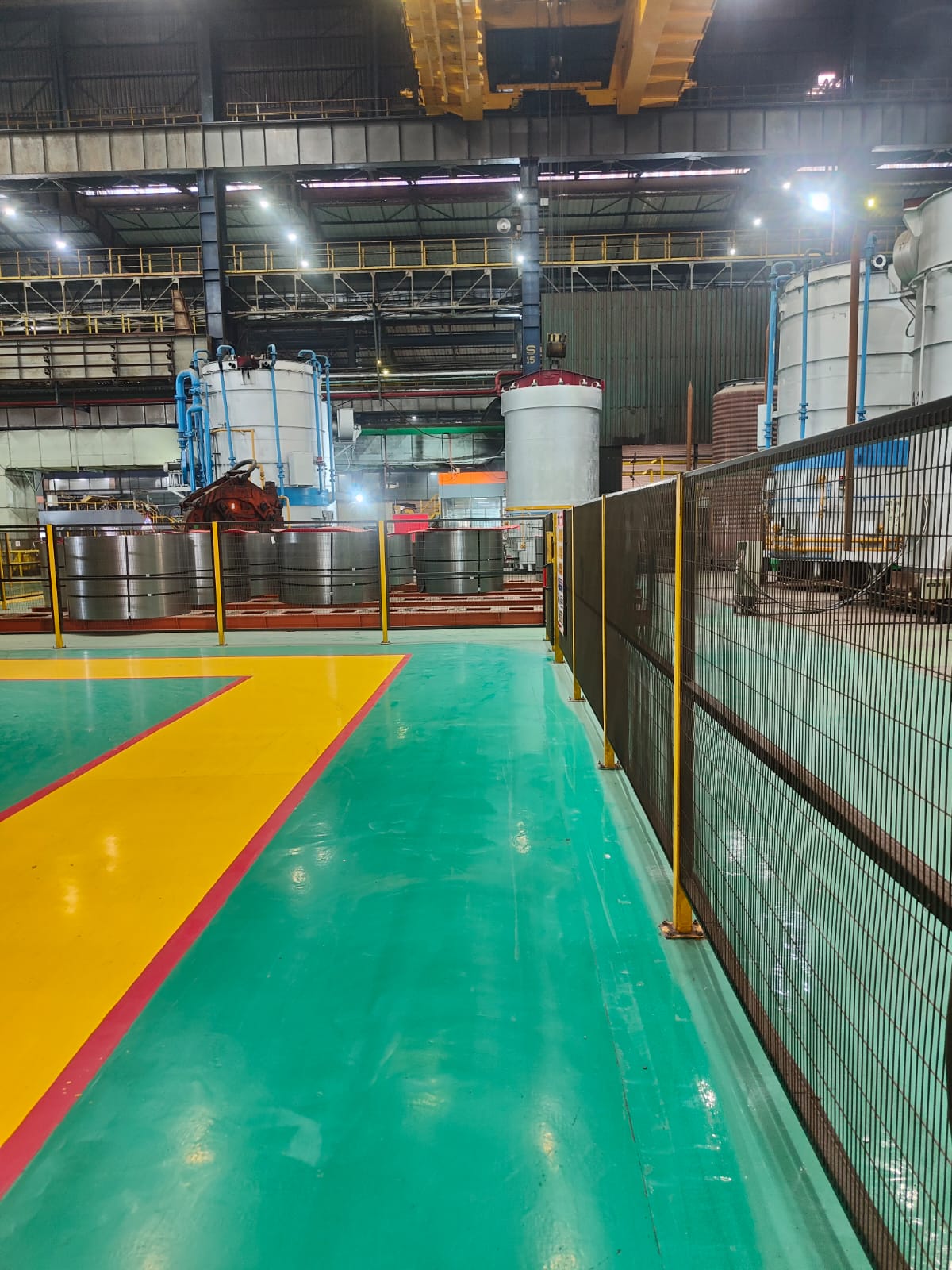
Safety guards, also known as machine guards or equipment guards, are physical barriers or protective devices designed to prevent contact with hazardous areas of machinery or equipment. These guards are essential for protecting workers from potential injuries caused by moving parts, electrical hazards, flying debris, and other dangers present in industrial or workplace environments. Here are some key aspects of safety guards:
Types of Guards:
- Fixed Guards: These guards are permanently attached to the machinery or equipment to enclose hazardous areas and prevent access to moving parts or other dangers.
- Adjustable Guards: Adjustable guards allow for flexibility in their positioning to accommodate different sizes of materials or machinery.
- Interlocking Guards: Interlocking guards are equipped with safety interlocks that automatically shut off the machine when the guard is opened or removed, preventing operation while the guard is not in place.
- Self-Adjusting Guards: Self-adjusting guards move with the machinery to maintain a safe distance between the operator and the hazardous area.
- Barrier Guards: Barrier guards create a physical barrier between the operator and the hazardous area, typically using materials such as wire mesh, plastic, or polycarbonate.
Safety Compliance:
- Occupational health and safety regulations often require safety guards to ensure compliance with safety standards. These regulations may specify the type of guards required, their design, and installation requirements.
- Compliance with safety standards such as those set by organizations like the Occupational Safety and Health Administration (OSHA) in the United States or the Health and Safety Executive (HSE) in the United Kingdom is crucial for maintaining a safe work environment.
Design Considerations:
- Safety guards should be designed to effectively prevent access to hazardous areas while allowing for visibility of the operation and maintenance tasks.
- Guards should be made of durable materials capable of withstanding impact and wear over time.
- Proper ventilation should be considered to prevent overheating of machinery while maintaining safety.
Training and Awareness:
- Proper training should be provided to workers on the use of safety guards, including their purpose, proper operation, and maintenance.
- Awareness campaigns and signage should be used to remind workers of the importance of using safety guards and following safety procedures.
Regular Maintenance and Inspection:
- Safety guards should be regularly inspected for damage, wear, or malfunction.
- Maintenance schedules should be established to ensure that guards are properly maintained and repaired or replaced as needed.
Integration with Safety Systems:
- Safety guards are often integrated with other safety systems such as emergency stop buttons, safety sensors, and warning alarms to provide comprehensive protection against accidents.
Leave a Reply
You Might Like Also
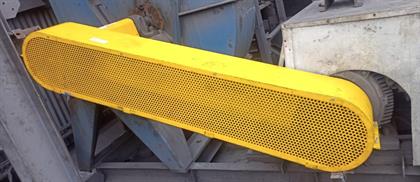
chain belt drive guard
May 06, 2024

pump coupling safety guard
May 06, 2024
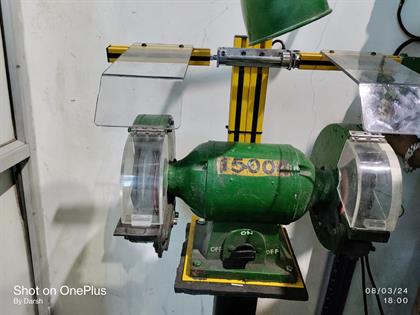
bench grinder machine safety guard
May 06, 2024
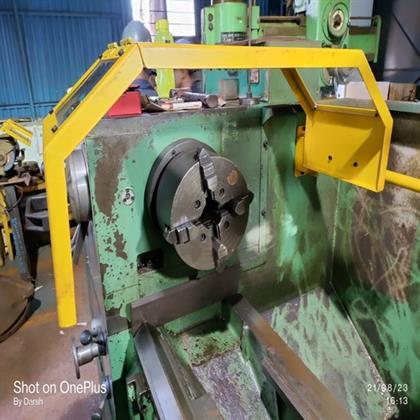
Lathe machine safety guard
May 06, 2024
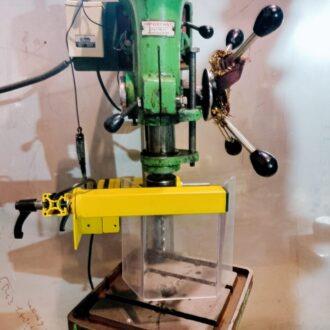
drilling machine safety guard
April 11, 2024
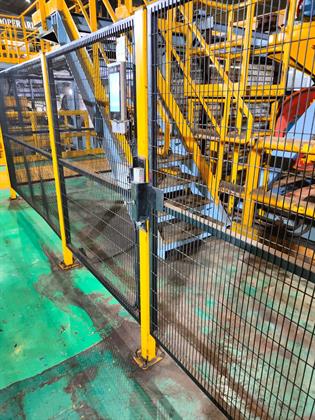
safety fence industrial
April 10, 2024